In production of sealing elements when a new product is taken in hand, productability in the manufacturer company’s conditions needs to be taken carefully; like at production of various parts, machine elements. When the company decides to produce a part, which suitable for it’s own manufacturing system, company takes care to conveniences at production of the part and producing the mould on designing stage. When it is thought for the product, in mould designing stage, minimum failure ratio comes into prominence. For the mould will be used multiple times and for multiple parts’ shaping; mould design must continue, therefore it’s repairing conditions, if there is an balk on mould or a part of the mould.
In mould designing initially conveniences at production of the part and then producion of the mould are considered. For having advantages in mould designing and using, the existing technology (usage of electro erosion discharge machines -EDM and WEDM- and CNC tool machines) must be used. While moulds that have simple and plain shaped can be processed by operator, who gives the coordinates; processing of complex shaped moulds are processed by the coordinates which is sent by CAD/CAM softwares.
To get an economical and efficient production, it is one of the preferred methods to use standard case model at mould designing. According to this method mould consists case, body and cases that embedded inside of bodies. At the situation that there is a failure on mould cases or/and moulded parts; only repairing or changing of cases decreases the cost losses, and it can be taken as the biggest advantage of this method. One of the things that has to be paid attention is not to apply so tight in the case.
If we summarize a mould production process;
- Design: To design the mould that have suitable and sufficient criterias for the production of sealing element (Material selection and cost analysis has to be taken on board.);
- Technical drawing: To draw the technical model, which has suitable dimensions and properties, for the obtainment of the mould;
- Material supplying: Kalıp için uygun görülen malzemenin elde edilmesi,
- Material supplying: To supply the right material for the mould;
- To process the rough finish on the mould:To process the mould for the values and properties on the technical drawing that had been drawn;
- To process the quenching, if it is needed for the chosen mould material;
- To process the last metal works on the mould including finishings, after quenching;
- Mould control: To control the mould’s dimensions, after the processing of finishing works, comparing with the one that is drawn before;
- First moulding control: To control and compare the product’s dimensions that is moulded after the mould is checked and approved, with the product’s dimensions which are aimed;
- Approval: To approve the mould, that is controlled, by authorized people;
- Production: To produce the approved mould at necessary quantity and through demands.
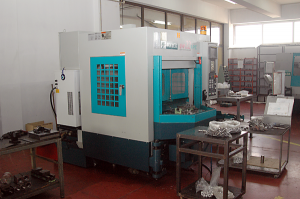
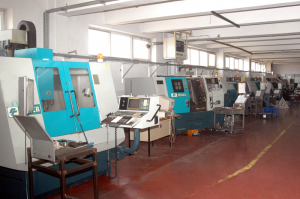